Exploring the Benefits and Limitations of Selective Laser Sintering of Metals and Ceramics
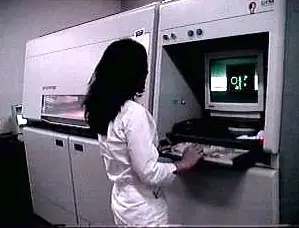
Selective Laser Sintering (SLS) is a 3D printing technology that has been used to produce parts from a variety of materials, including metals and ceramics. It is a form of additive manufacturing that works by using a laser to heat and fuse particles of a material together, layer by layer, to create a 3D object. The SLS process has been around since the 1980s and has been used in a wide range of industries, from medical to aerospace. In this article, we will explore the history of SLS, its development, and the process itself. We will also look at the various applications and uses of SLS.
Selective laser sintering (SLS) is a 3D printing technique that has been used since the late 1980s to create metal and ceramic parts. It was first patented in 1989 and the first machine was demonstrated in 1990. Since then, there have been numerous advances in the SLS process, such as the introduction of new materials, improved part accuracy, and increased build rates.
The SLS process involves a series of steps, including pre-treatment, powder bed formation, laser scanning, sintering, and post-treatment. This technology is used in a variety of industries, such as automotive, medical, and consumer product manufacturing. It is a reliable and cost-effective way to create complex parts and components with a high degree of accuracy and detail.
Selective Laser Sintering
The process involves several steps, such as pre-treatment, laser sintering, and post-processing. The automotive and medical industries are two of the most common applications of Selective Laser Sintering. Benefits of the process include high accuracy, low waste, and cost-effectiveness. The process is also advantageous due to its ability to produce complex shapes with a variety of materials. Additionally, the process is capable of creating parts with a high level of detail and strength. Selective Laser Sintering is a versatile process that can be used to produce parts for a wide range of applications. It is also an efficient process that can produce parts in a short amount of time. As the technology advances, the process will become even more efficient and cost-effective.
Applications And Uses
The Selective Laser Sintering (SLS) process is an additive manufacturing technology that is used in a variety of industries to produce a wide range of products. In the automotive industry, SLS is used to produce airbag covers, brake calipers, and gearbox components. In the medical industry, SLS is used to create medical implants and prosthetics, as well as dental crowns and bridges. In the aerospace industry, SLS is used to produce turbine blades and fuel nozzles. In the consumer products sector, SLS is used to produce hearing aids, eyeglass frames, and toys. Finally, SLS is used to produce intricate jewelry designs.
Advantages of SLS
Selective laser sintering (SLS) is a 3D printing technique that uses a high-power laser to fuse particles together to form a solid object. This process has been used for many years, but recent advances have made it more efficient. The steps involved in SLS include powder bed preparation, laser sintering, and post-processing. The automotive and medical industries have both benefited from the use of SLS, as it allows for the production of complex parts quickly and cheaply. The advantages of SLS include its cost-effectiveness, speed, and flexibility. However, there are also some limitations to consider, such as the need for post-processing and the limited range of materials that can be used.
In conclusion, selective laser sintering of metals and ceramics has a variety of advantages and limitations that must be considered when utilizing this technology. The high precision and accuracy, low cost of production, and ability to produce complex shapes make selective laser sintering a desirable choice for many applications. However, the long production times, limited range of materials, and relatively high energy consumption must be taken into account when deciding whether this technology is the right solution for a particular project. All in all, selective laser sintering of metals and ceramics is a complex process with both advantages and limitations that must be weighed carefully when selecting a manufacturing meth