Laser Peening: Techniques and Fundamentals
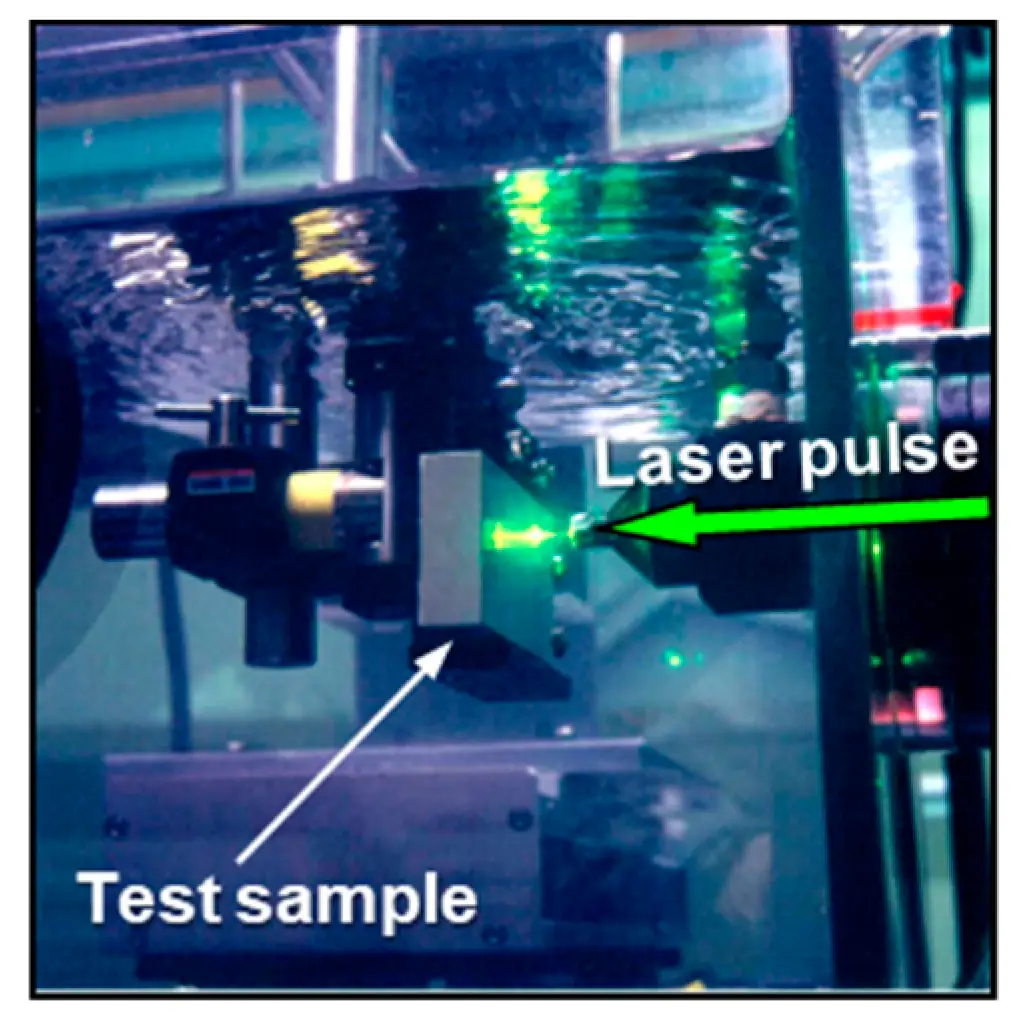
The Science of Laser Peening is an ever-evolving field that has revolutionized various industries, particularly in the realm of material enhancement. This advanced process involves using high-powered laser pulses to impart compressive residual stresses on the surface of metallic components. In this article, we will delve into the techniques and applications of laser peening, providing you with a comprehensive understanding of this cutting-edge technology.
The Fundamentals of Laser Peening
Laser peening is a surface modification technique that improves the fatigue life, wear resistance, and stress corrosion cracking resistance of metal components. By inducing compressive residual stresses into a material’s surface, it enhances the mechanical properties and overall performance.
The process begins with a high-powered, short-pulse laser beam directed at the material’s surface. A thin layer of protective coating or a tamping medium, such as water, is applied to prevent surface damage from the laser pulse. The laser energy absorbed creates a plasma, which generates a shockwave that propagates into the material. The shockwave induces compressive residual stresses, which can extend several millimeters into the surface.
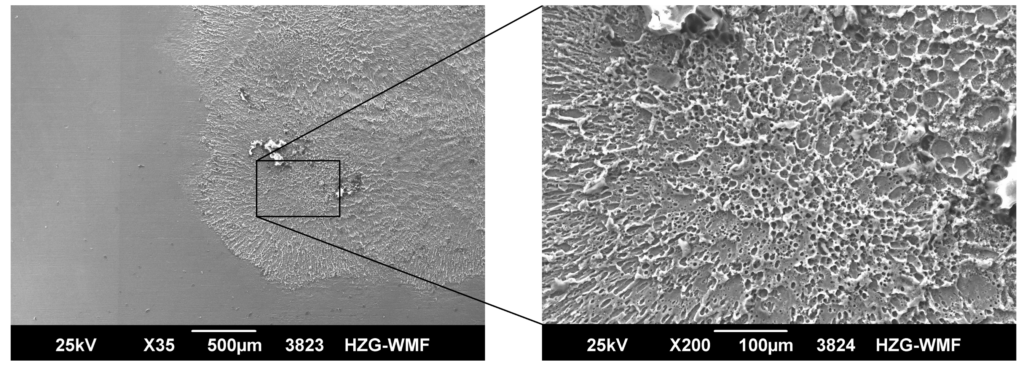
Key Techniques in Laser Peening
Laser peening encompasses various techniques to cater to different material types and applications. Understanding these methods is essential for choosing the most suitable approach. We will discuss two primary techniques in laser peening: dry and wet peening, as well as two secondary methods: multi-pulse and dual-beam peening.
- Dry Peening: In this technique, a transparent overlay (such as a sacrificial glass or plastic) is placed on the metal surface, protecting it from potential laser-induced damage. The overlay absorbs the laser energy and creates a plasma, which generates the shockwave required for peening. Dry peening is beneficial in situations where water or other tamping media are not suitable due to environmental or logistical constraints. However, it may not provide the same depth of compressive residual stresses as wet peening.
- Wet Peening: This method utilizes a thin layer of water or another tamping medium to protect the material’s surface during peening. The water layer absorbs the laser energy and creates a plasma, generating the shockwave that induces compressive residual stresses. Wet peening is the more common method, as the water helps absorb and dissipate the heat generated during the process, reducing the risk of surface damage and providing deeper compressive residual stresses than dry peening.
- Multi-Pulse Peening: In certain applications, it may be necessary to use multiple laser pulses on the same area to achieve the desired results. Multi-pulse peening increases the depth and magnitude of the compressive residual stresses, allowing for improved fatigue life and stress corrosion cracking resistance. This technique requires precise control of the laser parameters and the timing between pulses to avoid unwanted surface damage.
- Dual-Beam Peening: This advanced technique involves using two separate laser beams to create overlapping plasma zones on the material’s surface. The interaction between the two plasma zones generates a combined shockwave with increased intensity and duration, which can induce even deeper compressive residual stresses. Dual-beam peening offers the potential for further enhancement of material properties, but it requires sophisticated equipment and precise control of the laser parameters.
By understanding these various techniques, engineers and material scientists can optimize the process for specific materials and applications, achieving the best possible results in terms of material enhancement and component performance.
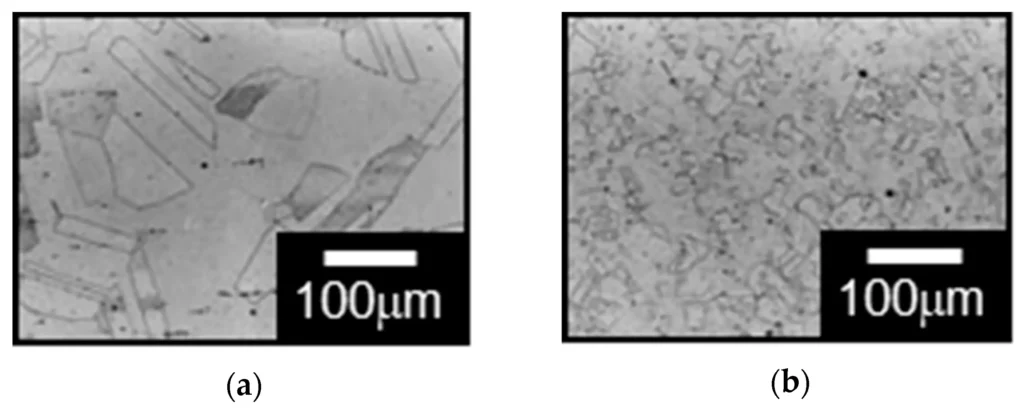
Types of Lasers Used for Peening
The effectiveness of laser peening depends not only on the technique but also on the type of laser used. Different lasers offer varying pulse durations, power levels, and wavelengths, affecting the depth and magnitude of the induced compressive residual stresses. Here, we explore some of the most common types of lasers employed in laser peening:
- Nd:YAG Lasers: Neodymium-doped Yttrium Aluminum Garnet (Nd:YAG) lasers are among the most widely used for laser peening applications. These solid-state lasers offer high peak power and short pulse durations, typically ranging from a few nanoseconds to several hundred nanoseconds. Nd:YAG lasers emit light with a wavelength of 1,064 nm in the near-infrared region, which is suitable for many metallic materials.
- Fiber Lasers: Fiber lasers have gained popularity in recent years due to their exceptional beam quality, high energy efficiency, and compact size. These lasers operate using an optical fiber doped with rare-earth elements, such as erbium or ytterbium. With pulse durations typically in the picosecond to nanosecond range, fiber lasers can provide the high peak power required for effective laser peening.
- Excimer Lasers: Excimer lasers use a mixture of noble gases and halogens to create a high-energy, ultraviolet (UV) laser beam. Although not as common as Nd:YAG or fiber lasers for laser peening, excimer lasers can be used for specific applications where a UV wavelength is more effective at inducing compressive residual stresses. These lasers have shorter pulse durations, typically in the nanosecond to picosecond range, which can result in more localized peening effects.
Each type of laser has its advantages and limitations, and the choice of laser depends on factors such as the material being processed, the desired depth and magnitude of residual stresses, and the specific application requirements. By understanding the capabilities and constraints of different lasers, engineers and researchers can optimize the laser peening process to achieve the best possible results.
Applications Across Industries
Laser peening has found its way into various industries, including aerospace, automotive, power generation, medical, and even oil and gas. Some notable applications include:
- Aerospace: Enhancing fatigue resistance and preventing stress corrosion cracking in aircraft components, such as turbine blades, landing gear, and airframe structures, is critical for flight safety. Laser peening can extend the service life of these components by improving their mechanical properties, resulting in reduced maintenance costs and increased operational efficiency.
- Automotive: Laser peening can increase the wear resistance of engine components, such as camshafts, gears, and connecting rods, which helps to reduce maintenance costs and extend the life of vehicles. Additionally, lightweight materials used in the automotive industry, such as aluminum and magnesium alloys, can benefit from laser peening to improve their strength and fatigue resistance.
- Power Generation: In the power industry, laser peening has been used to improve the performance of steam and gas turbine components, such as turbine blades, rotors, and casings, as well as nuclear reactor pressure vessels, by mitigating stress corrosion cracking and enhancing fatigue life. This leads to increased efficiency, lower maintenance costs, and extended component lifetimes in power plants.
- Medical: The medical industry utilizes laser peening to enhance the durability and wear resistance of orthopedic implants, such as knee and hip replacements, dental implants, and spinal fusion devices. By improving the mechanical properties of these implants, patients experience longer-lasting solutions with reduced chances of implant failure and subsequent revision surgeries.
- Oil and Gas: The harsh environments encountered in the oil and gas industry demand components with high resistance to wear, corrosion, and fatigue. Laser peening can be applied to critical components, such as drilling equipment, pipelines, and valves, to enhance their durability and reduce the risk of failures, which can have significant environmental and economic consequences.
- Maritime: The maritime industry can benefit from laser peening applications on components exposed to corrosive marine environments. It can also be used to increase the corrosion resistance and fatigue life of ship hulls, propellers, and other critical components, resulting in reduced maintenance costs and increased vessel longevity.
- Manufacturing and Tooling: The manufacturing industry relies on tools and dies that endure high levels of stress and wear. Laser peening can enhance the performance and lifespan of these tools by increasing their resistance to wear and fatigue, ultimately leading to lower production costs and higher-quality products.
As laser peening technology continues to advance, its applications across various industries are expanding. With ongoing research and development, we can expect to see even more innovative uses for this groundbreaking process, benefiting not only the industries mentioned above but also paving the way for new opportunities in emerging sectors.
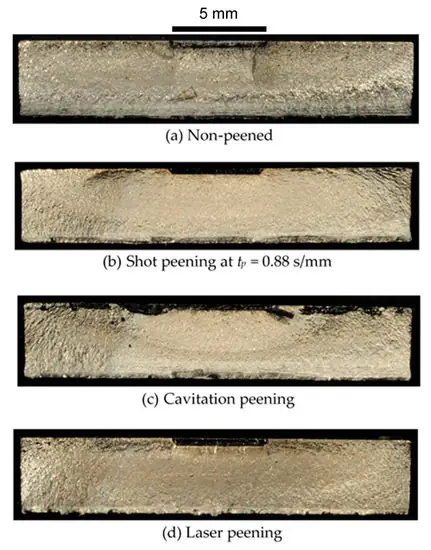
The Future of Laser Peening
The science of laser peening continues to evolve, with ongoing research and development paving the way for new techniques and applications. As our understanding of material science and laser technology deepens, we can expect to see even more innovative uses for this groundbreaking process, benefiting various industries and improving the lives of countless individuals.