Laser Shock Peening: Applications, Benefits, and Limitations
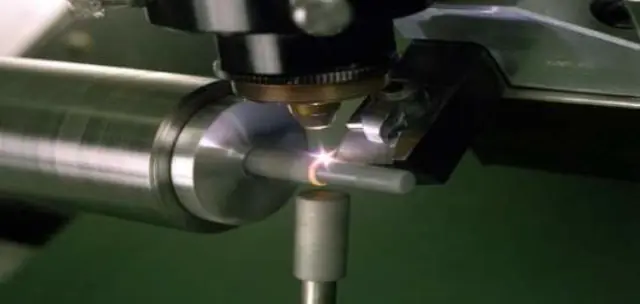
Manufacturing has always been a critical aspect of society, and over the years, advancements in technology have improved the efficiency and effectiveness of manufacturing processes. One of the more recent innovations in manufacturing is laser shock peening, which has been gaining popularity due to its ability to improve mechanical properties, increase durability, and reduce residual stress in materials. In this article, we will explore laser shock peening, its applications, benefits, limitations, and future prospects.
How Laser Shock Peening Works: Understanding the Physics
Laser shock peening is a surface treatment technique that uses high-energy laser pulses to create a shockwave on the surface of a material. The shockwave induces plastic deformation and compressive residual stresses in the material, which can enhance its mechanical properties. The process involves the generation of plasma on the surface of the material, followed by the rapid expansion of the plasma, which creates the shockwave. Compared to traditional shot peening, laser shock peening is more precise and can be tailored to the specific needs of a material or component.
Applications Of Laser Shock Peening in Various Industries
Given its numerous benefits, it has found applications in various industrial sectors, including aerospace, automotive, medical, and energy. In the aerospace industry, it can improve the fatigue life of critical components like turbine blades, compressor blades, and engine components, which are subject to high stress loads and extreme temperature variations. The technique has been used to improve the performance and durability of different aircraft components and systems, including landing gears, wing spars, and helicopter rotors.
The technique can be used by the automotive industry to increase the durability and fatigue life of engine and transmission components, such as crankshafts, camshafts, connecting rods, and gears. The resulting improvement in mechanical properties can lead to more efficient and reliable vehicles with longer service life.
In the medical industry, it can improve the biocompatibility of medical implants by creating a surface with improved mechanical properties and reduced roughness. The improved mechanical properties of the implant can enhance the implant’s durability and stability, while the reduction in roughness can prevent bacterial adhesion, reducing the risk of infection.
The technique can improve the performance and longevity of materials used in power generation and transmission by the energy industry, such as gas turbine blades, steam turbine blades, and boiler tubes. By enhancing the mechanical properties of these materials, the technique can help reduce maintenance costs, minimize downtime, and increase the efficiency and reliability of power generation systems.
Advantages Over Traditional Surface Treatment Techniques
Laser shock peening offers many advantages over traditional surface treatment techniques. First, it can significantly increase the fatigue life of components, making them more reliable and durable. Second, it can increase resistance to corrosion and cracking, which is particularly important in harsh environments. Third, it can reduce surface roughness, improving the aesthetic appearance of components. Finally, it can reduce material residual stress, which can improve the performance and longevity of components.
Challenges and Limitations of Laser Shock Peening
The high equipment and maintenance costs associated with the technique are one of the most significant challenges. Achieving uniform coverage, particularly on complex geometries, can also be challenging. Moreover, the lack of standardization in process parameters can make it difficult to compare results across different studies.
Future Developments and Potential Improvements
As manufacturers continue to seek out new ways to enhance the durability and performance of their components, laser shock peening is emerging as a promising technique. Despite the challenges it presents, including high costs and the difficulty of achieving uniform coverage on complex geometries, it’s expected to grow in popularity in the years to come.
One factor driving this growth is the ongoing development of laser technology. Advances in ultrafast lasers and other laser sources are making it more affordable and accessible. Furthermore, researchers are exploring the use of new materials specifically designed for laser shock peening, which could result in even greater improvements in mechanical properties.
Conclusion: A Promising Future for Manufacturing
Laser shock peening is a powerful surface treatment technique that offers many advantages over traditional surface treatment techniques. Although there are challenges and limitations, ongoing advances in technology and materials are likely to make it an increasingly important tool for improving the performance and longevity of critical components across various industries. As such, it holds a promising future in manufacturing.