The Selective Laser Sintering (SLS) 3D Printing Process
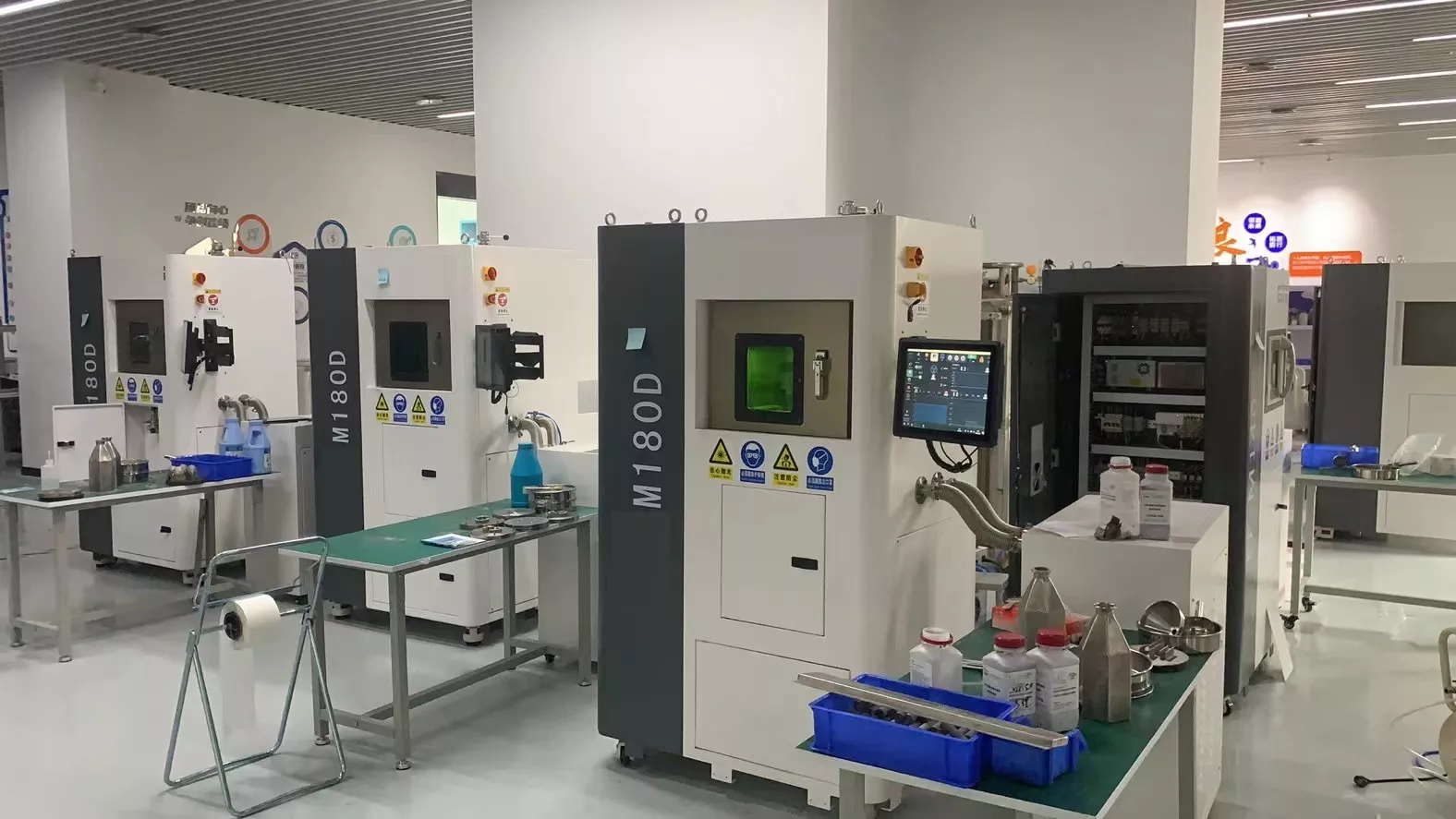
Selective laser sintering (SLS) is an additive manufacturing (AM) technique that uses a laser to fuse together small particles of plastic, metal, or ceramic powder into a three-dimensional (3D) object. The laser selectively fuses the powder particles together by scanning the cross-section of the desired object layer-by-layer. SLS is similar to another AM technique called selective laser melting (SLM), but in SLS the laser does not completely melt the powder particles, but rather just enough to fuse them together. This allows SLS to be used with a wider range of materials, including those that cannot be melted without degrading their properties, such as certain plastics and ceramics.
SLS was invented in the early 1980s by Dr. Carl Deckard and Dr. Joe Beaman at the University of Texas at Austin. It was originally developed as a way to rapidly prototype parts for use in injection molding and other manufacturing processes. SLS quickly gained popularity in a wide range of industries due to its ability to produce strong and complex parts from a variety of materials. Today, SLS is used in a wide range of applications, including prototyping, low-volume production, and even direct-digital manufacturing (DDM).
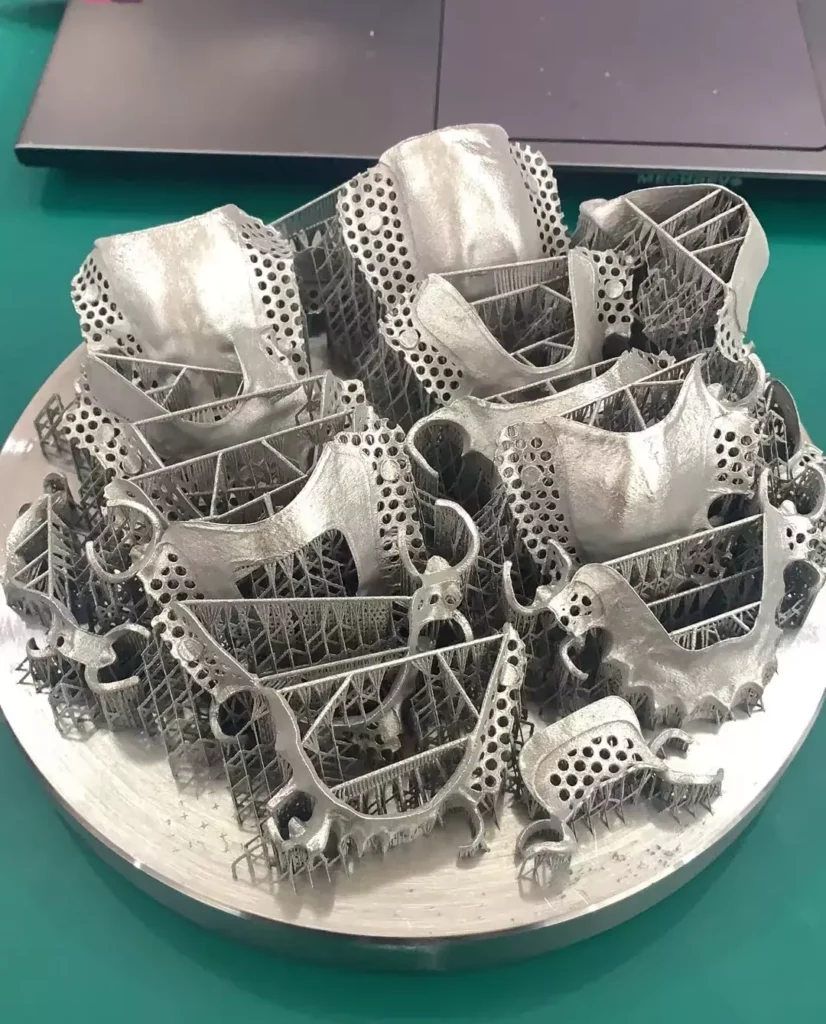
Lasers play a critical role in the SLS process, and there are a variety of different types that can be used. The most common type of laser used in SLS is a carbon dioxide (CO2) laser, which can be used to fuse a wide range of powder materials. CO2 lasers are typically used for larger parts or for applications where high accuracy is required. Other types of lasers that can be used include fiber lasers and excimer lasers. These lasers are typically used for smaller parts or for special applications where very high accuracy is required.
Excimer lasers are another type of laser that can be used in SLS, but they are less common due to their high cost. Excimer lasers emit ultraviolet (UV) light instead of infrared light like CO2 and fiber lasers. This UV light is absorbed by almost all materials, which makes excimer lasers very versatile. Excimer lasers are typically only used for special applications where other types of laser cannot meet the requirements.
The SLS process begins with a 3D CAD model of the desired part. This model is then used to generate a layer-by-layer cross-sectional view of the part, which is sliced into thin layers typically ranging from 20 to 100 microns thick. A build platform is then coated with a layer of powder material, and the first slice is projected onto the powder using a laser. The laser selectively fuses the powder particles together according to the cross-sectional profile of the slice. The build platform is then lowered by one slice thickness and another layer of powder is applied. This process is repeated until the entire part has been built.
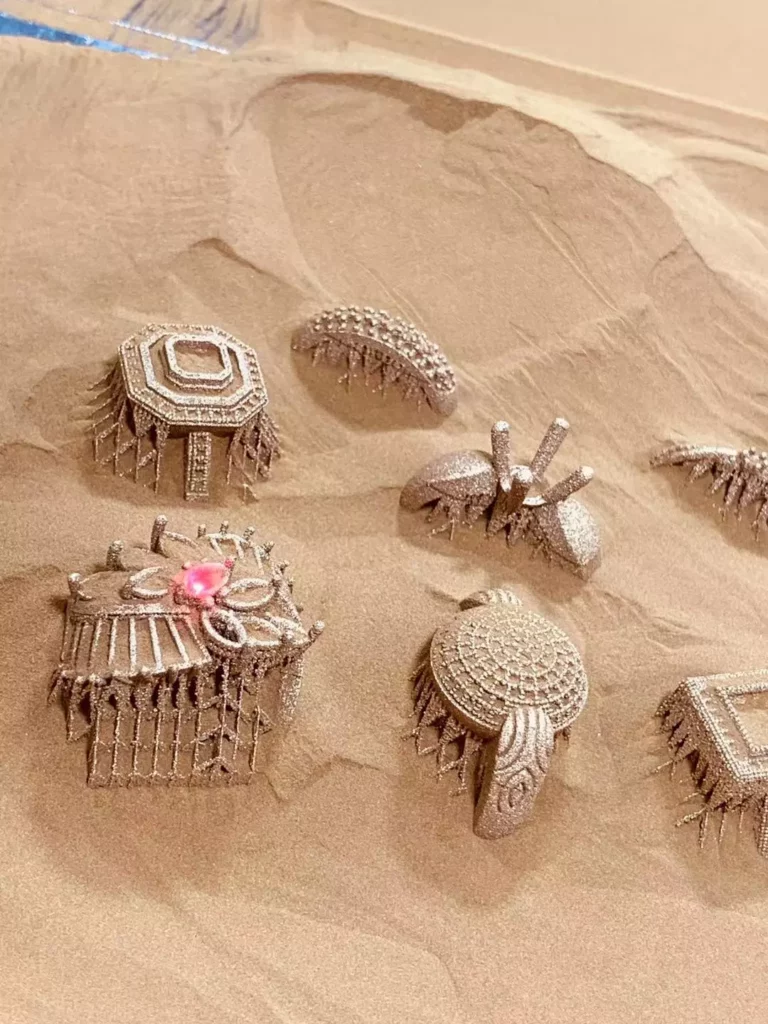
Once the build is complete, any excess powder is removed and the part is cooled. The final step is to remove any supports that were used during the build process to prevent collapse or distortion of overhanging features. The completed part can then be used as-is or undergo post-processing steps such as painting, plating, or machining.
SLS offers a number of advantages over other AM processes, including its ability to use a wide range of materials, its high accuracy and repeatability, and its relatively low cost. Additionally, SLS parts do not require support structures, which means that they can have complex geometries that would be impossible to produce using other methods.